Liner Hanger Systems Installation Failures
30 May 2016 I am working on liner hanger. The company I work in experienced many failures when trying to install them (5 failures on the last 5 jobs). The failures concerns a sequence in the procedure:- The packer which could not be set
- the drill pipe dart which didn't land on the wiper plug
- the wiper plug which didn't shear, so didn't bump on the landing collar.
I would like to have advice from others concerning root causes of such kind of incidents.
6 Answer(s)
PLEASE LOGIN OR SIGN UP TO JOIN THE DISCUSSION
Support Spread
We need the support of our members to keep our forum online. If you find the information on spread useful please consider a donation

Posted by

KAMDEM Morel
Intern
Discussions: 1
Replies: 0
Related Discussions
Drilling 8 1/2" hole out of 20" shoe
37" HoleOpeners
Flexjoint wearbuushings
Clearing site for landrigs
Thru tubing fishing
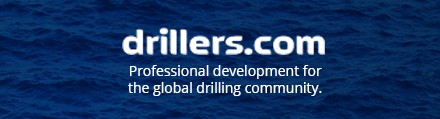
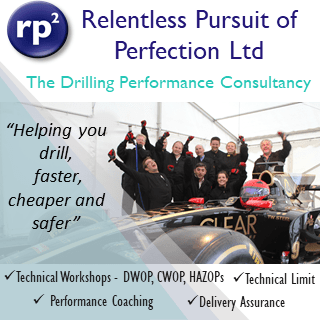