Who is responsible for ROP performance
13 June 2018 Is there any study to quantify the responsibility of each contributor to ROP (or Feet per day)?There are many contributors: rig company, directional drilling company, operator or well owner...
6 Answer(s)
PLEASE LOGIN OR SIGN UP TO JOIN THE DISCUSSION
Support Spread
We need the support of our members to keep our forum online. If you find the information on spread useful please consider a donation

Posted by

Baraket Mehri
Head of D&WO Real Time Ops Center
Discussions: 1
Replies: 0
Related Discussions
Drilling 8 1/2" hole out of 20" shoe
37" HoleOpeners
Flexjoint wearbuushings
Clearing site for landrigs
Thru tubing fishing
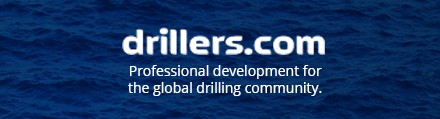
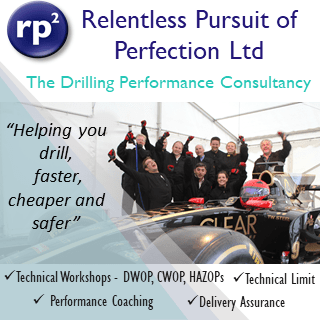