Non Return Valves with MPD
11 January 2019Non Return valves in MPD operations are to be non ported and pressure tested before use.
The reason for this is that with applied annular pressure applied, drillstring connections cannot be made if the float valves are leaking.
During a
recent HAZOP planning for a constant bottom hole pressure MPD operation, the operator highlighted that in the past they had experienced float valve
failures even with two floats in the drillstring. This resulted in the question
how many float valves do we need in the string.
This raises some additional interesting questions
How many floats are run in the string when drilling with MPD using constant bottom hole pressure
Are float valves shipped from shore complete with test certificates and inspection reports
Are used floats be re-dressed on the rig, if they are, are the redressed floats pressure tested on the rig and to what pressure. Who tests and who is the witness on the test.
Are floats in the string changed every time there is a trip back to surface to make a bit change
If not how long are floats used in the string
Love to hear from service providers and operators of any failures and current practices.
5 Answer(s)
PLEASE LOGIN OR SIGN UP TO JOIN THE DISCUSSION
Support Spread
We need the support of our members to keep our forum online. If you find the information on spread useful please consider a donation

Posted by
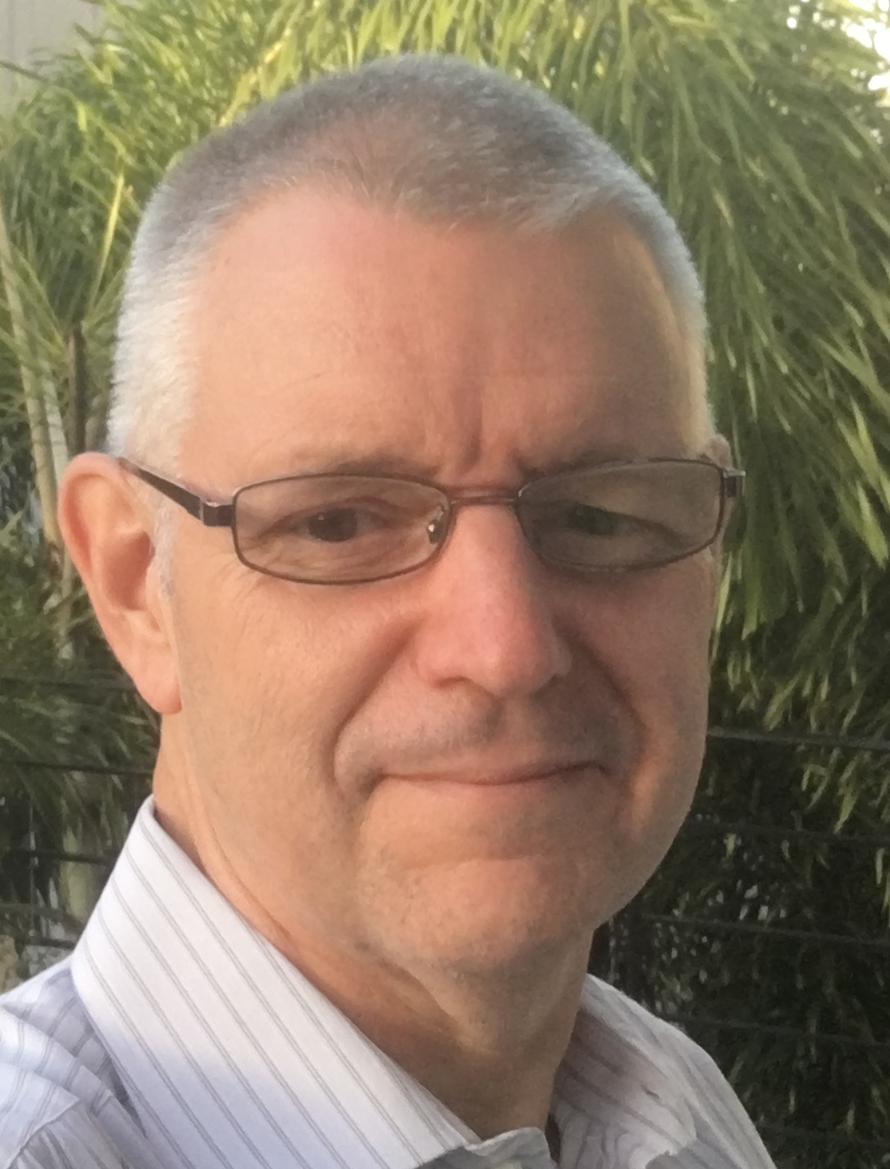
Steve Nas
Wells Mgr - Wellspec
Discussions: 5
Replies: 63
Related Discussions
Sacrifice fluid (water) in PMCD HPHT
Underbalanced Torque and Drag
Rotating Control Heads
RMR system for the wells in >600m water depth
Regarding Top kill -recommended practice,successes or anything similar
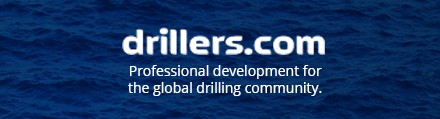
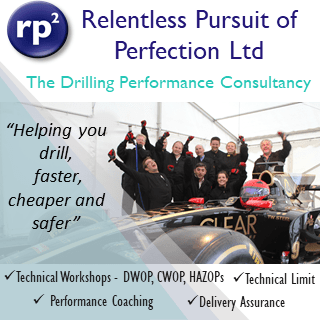