Experiences with bow centralisers on semi-flush Q-125 pipe
23 March 2009 In context, the story goes like this. We are looking to use a standard GoM (sub-salt) well design around the world with a deepwater drillship. Rather than chop and change casing designs we see a merit in keeping casing sizes/grade/connection constant (even though all strings below 22in are either semi-flush or flush). An obvious downside is when a particular well design doesn't require all the casing strings and here, specifically, we have no need per se for centraliser subs and bows would do.However, the 2 questions I have are:-
1. Have folk run bows on semi-flush/flush pipe and seen problems and, if so, what...i.e was the solution that subs had to be used or a change to the bow fastening ?
2. Conventionally 1 stop collar either is used. Given hard "Q" grade, is there any experience suggesting 2 stop collars might be advantageous i.e. double chance of stop screws 'biting/binding' the casing ?
Thanks
Mike
Hess, GoM
9 Answer(s)
PLEASE LOGIN OR SIGN UP TO JOIN THE DISCUSSION
Support Spread
We need the support of our members to keep our forum online. If you find the information on spread useful please consider a donation

Posted by

Mike Nippard
Discussions: 2
Replies: 1
Related Discussions
Light Weight Cement for Structural Casing
Cementing 30" With No Vent Valve
Cementing through Tesco Casing Running Tool
Cement mule shoe
Displacing liner cement with water to suspend
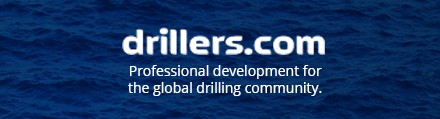
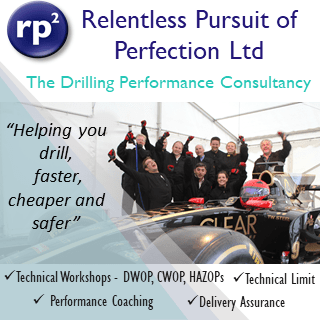