How to avoid multistage cement operations in long intervals of casing?
30 June 2019 Dear colleagues,The standard practice in our company is to run intermediate 9 5/8" casing in one string, but cement them in two stages with stage tool and production 7" casing is usually run in two strings (liner with tie- back).
Due to the last time failure with stage tool, the one of the primary targets for our team is to eliminate stage cementing or tie- back liner approach and apply advanced cement technology for our next wells.
The challenge is to cement casing in one stage up to the surface, without losses or formation fracturing and preferably without reducing cement integrity in HPHT environment.
Information for intermediate 9 5/8" casing
1. Depth 4670m2. Temperature at the bottom up to 125 Celsius
3. Formation pressure 8100 psi
4. Previous casing shoe 2250m (with LOT pressure 5000 psi)
5. WBM, mud weight 1.25spg
Information for 7"production casing
1. Depth 5400m
2. Temperature at the bottom up to 155 Celsius
3. Formation pressure 14 500 psi
4. Previous casing shoe 4670m
5. WBM, mud weight 1.90spg
In both cases the cement slurry should be pumped up to the surface according to the requirements of local legislation for gas wells.
So, my question is:
Does anybody have an experience doing cement job in one run in similar conditions?
I would
appreciate if you could share with us which technology did you use?
Best regards,
Viktor
5 Answer(s)
PLEASE LOGIN OR SIGN UP TO JOIN THE DISCUSSION
Support Spread
We need the support of our members to keep our forum online. If you find the information on spread useful please consider a donation

Posted by

Viktor Sieryi
Drilling engineer
Discussions: 1
Replies: 0
Related Discussions
Light Weight Cement for Structural Casing
Cementing 30" With No Vent Valve
Cementing through Tesco Casing Running Tool
Cement mule shoe
Displacing liner cement with water to suspend
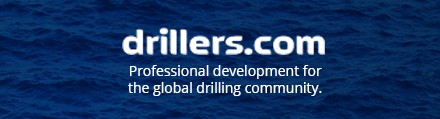
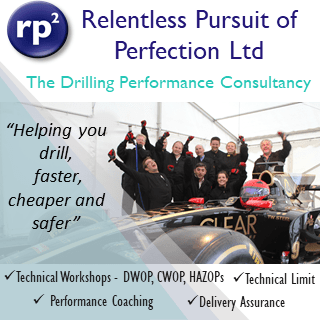