Managing of overpull issues/the best drilling practices
08 July 2019 Dear forum members I have 3 questions with regard to modern drilling practices: 1.Wiper trips practices We are trying to avoid excessive wiper and check trips when there is no need for one in our local land operations in Ukraine. In the past we would do check trips every 200m regardless of the hole conditions. However we understand that at some point we have to do check trips, for instance when there are excessive overpulls or before running the casing or wireline etc. We would like to hear what are your practices for wiper trips? When do you normally decide to do one? Are there any numbers you are guided by, like overpulls? 2. Connections practice We also would like to hear what connection practices are you generally applying in your operations and why. For reference, we drill one stand and wipe the hole up and down once to the distance of one drill pipe while circulating cuttings above BHA. We try not to backream to avoid shale breakouts upper in the hole. 3. Backreaming What is your practice for backreaming? Are you trying to avoid it whenever possible or not and why. I understand much will depend on local geological conditions but still would like to hear your general approaches. Appreciate your thoughts. Regards Denys4 Answer(s)
PLEASE LOGIN OR SIGN UP TO JOIN THE DISCUSSION
Support Spread
We need the support of our members to keep our forum online. If you find the information on spread useful please consider a donation

Posted by

Denys Holub
Well preparation and design manager
Discussions: 3
Replies: 3
Related Discussions
Milling through a casing collar
With this down turn in our industry are multilaterals a useful well construction technique to reduce costs?
Expert Training Support Offer : How the Latest ERD Innovations Can Benefit Your Deviated Wells
How to remember everything you have ever learned.
Coiled tubing bridge plug milling
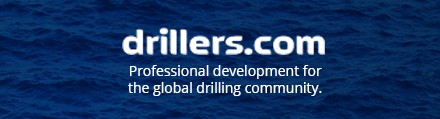
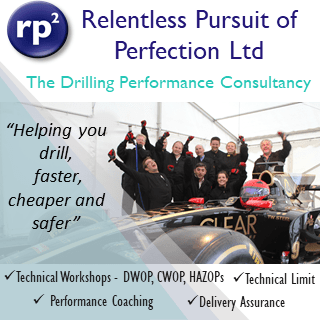