Large bore production casing
26 July 2019Hi to All.
I would like to share with you a possible casing design for a Deep-water Development well for a shallow gas reservoir.
Usually the standard casing design are the following:
36” jetting
20”-Swedge-13 5/8”
9 5/8” – 10 ¾”
open hole /GP
Upper Completion (UC)
Looking to the new gas tight 20” connectors, it might possible to remove a string from the well architecture, by incorporating a casing design MTM (Metal-to-Metal) as following:
36” jetting
20” MTM ( gas tight 6500 psi burst) -Swedge-13 5/8” MTS ( gas tight )
Liner 9 5/8”
open hole /GP
UC
I would like to ask you if any team in the world has implemented (or is close to implementing) a design like this: production tubing run inside the 20” gas tight casing.
Things like wellhead and tree design also spring to mind.
If anyone has some feedback, it would be greatly appreciated.
Thx
2 Answer(s)
PLEASE LOGIN OR SIGN UP TO JOIN THE DISCUSSION
Support Spread
We need the support of our members to keep our forum online. If you find the information on spread useful please consider a donation

Posted by
Ibrahim Luciano Salis
WCM SN Drilling and Completion SPT
Discussions: 1
Replies: 0
Related Discussions
Milling through a casing collar
With this down turn in our industry are multilaterals a useful well construction technique to reduce costs?
Expert Training Support Offer : How the Latest ERD Innovations Can Benefit Your Deviated Wells
How to remember everything you have ever learned.
Coiled tubing bridge plug milling
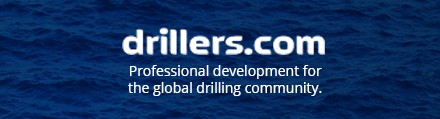
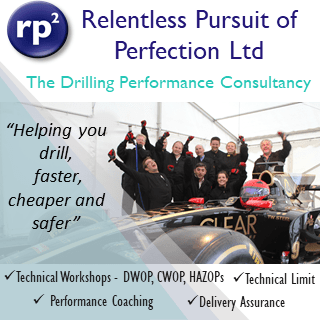