How to get weight to the bit in a long, horizontal lateral well?
06 September 2019 I am curious as to how weight on bit is applied in a long horizontal well. I have been involved in extended reach wells and wells with complex well paths, but never been involved with the long horizontal laterals which I have been reading about lately.When your standard BHA/Drill Collars pass the bend section, the weight of the collars is then transferred to the low side of the hole and do not provide any weight to the bit. Granted, you can reconfigure your drill string to place the collars and heavy weight drillpipe back in the vertical section of the well, but this causes derrick management issues during tripping as well as buckling concerns in the drillstring now below the collars.
Furthermore, at some point, regardless of the collar weight you have in the vertical section, as the horizontal section is extended, drag would 'eat up' any weight which was efectively transferred through the build up section.
If anyone could give me a 'quick & dirty' tutorial on how weight is transferred to the bit in a long horizontal section it would be greatly appreciated!
3 Answer(s)
PLEASE LOGIN OR SIGN UP TO JOIN THE DISCUSSION
Support Spread
We need the support of our members to keep our forum online. If you find the information on spread useful please consider a donation

Posted by
Douglas Buckland
Drilling Consultant
Discussions: 1
Replies: 0
Related Discussions
Drilling 8 1/2" hole out of 20" shoe
37" HoleOpeners
Flexjoint wearbuushings
Clearing site for landrigs
Thru tubing fishing
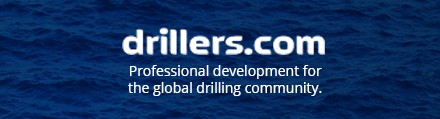
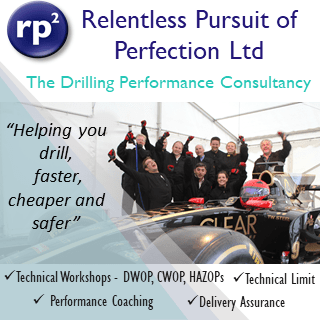