Casing Magnetization
12 December 2019 Hello,We are assessing the impact of magnetized casing (mitigation for relief well / PMR in salt) on the drilling operation:
- Handling / storage: interference with MHWirth (pipe handling), rig floor gauges and sensors, rig cameras
- Interference with Torque Turn Computer during M/U
- Interference with LWD tools (hot spot creation on the BHA). THIS IS OUR MAIN FEAR
For this of you with experience of handling and running magnetised casing, or who have encountered the concerns above, we'd be delighted to hear from you.
Merci
Florian
3 Answer(s)
PLEASE LOGIN OR SIGN UP TO JOIN THE DISCUSSION
Support Spread
We need the support of our members to keep our forum online. If you find the information on spread useful please consider a donation

Posted by
Florian Mercier
Drilling Engineer
Discussions: 2
Replies: 1
Related Discussions
Milling through a casing collar
With this down turn in our industry are multilaterals a useful well construction technique to reduce costs?
Expert Training Support Offer : How the Latest ERD Innovations Can Benefit Your Deviated Wells
How to remember everything you have ever learned.
Coiled tubing bridge plug milling
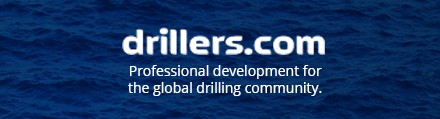
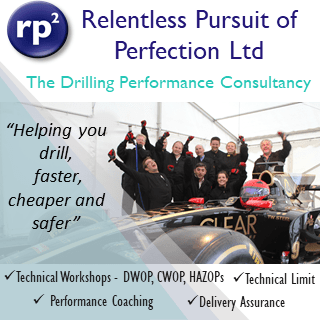