Inflow testing with a shallow packer
24 March 2020Colleagues,
I need help in either convincing my colleagues that I am right, or help understanding why I am wrong. In question is what happens below a packer when doing an inflow test when the hydrostatic in the annulus below the packer exceeds the hydrostatic inside the drillstring. Consider the example below (and shown in the attachment):
1. The well contains 12.0ppg mud.
2. Open-ended drillpipe is run to 2000mRT, with a packer high up in the string at 200mRT.
3. The drillpipe is displaced to 2000m with 8.5ppg seawater with a surface U-tube pressure of 1194psi.
4. The packer is set.
5. The U-tube pressure on top the drillpipe is bled off and the drillpipe left open to the atmosphere.
6. What happens next?
I maintain that the mud in the annulus below the packer will backflow up the drillpipe until equalized, leaving a void below the packer with a pressure of zero (gauge) below the packer, and on top of the mud.
My colleagues, who are experienced engineers, maintain that the mud on the backside would remain stationary since there is nothing to fill the void below the packer that would be created if the mud U-tubed away. The pressure below the packer would have to be negative, or I suppose zero (but without a void create by equalization). Neither of those outcomes seem possible to me.
Their argument is that this is the way inflow tests have always been done. But I maintain that this could only be done (without backflow) if the packer is set deep enough so that the hydrostatic in the annulus below the packer is less than the hydrostatic inside the drillpipe.
Any views?
Also, could anyone help me to understand why the pressure inside the void below the packer would only go down to zero (gauge), and not create a vacuum (of negative gauge pressure)?
Thanks for your help.
Paul Boudreau
paulboudreau@yahoo.com
Documents uploaded by user:
Inflow Test with Shallow Packer.pdf
13 Answer(s)
PLEASE LOGIN OR SIGN UP TO JOIN THE DISCUSSION
Support Spread
We need the support of our members to keep our forum online. If you find the information on spread useful please consider a donation

Posted by
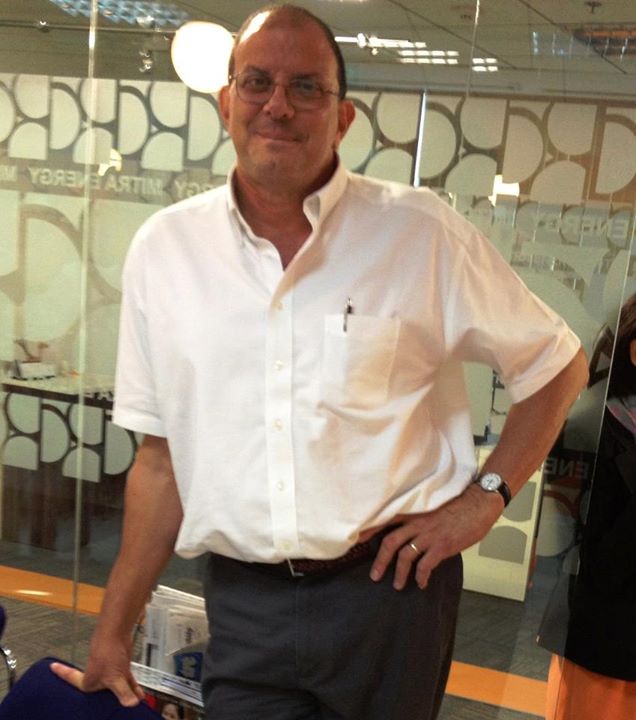
Paul Boudreau
Deepwater SDE
Discussions: 1
Replies: 7
Related Discussions
Milling through a casing collar
With this down turn in our industry are multilaterals a useful well construction technique to reduce costs?
Expert Training Support Offer : How the Latest ERD Innovations Can Benefit Your Deviated Wells
How to remember everything you have ever learned.
Coiled tubing bridge plug milling
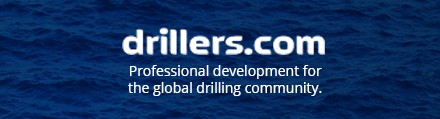
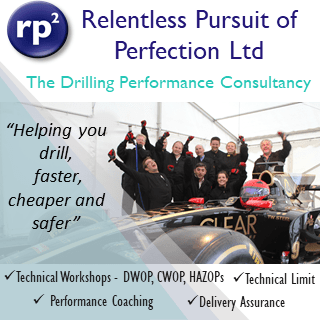