Deep Water Coil Tubing Sand Clean Out
12 May 2020We are looking at options for doing deepwater sand clean outs with coil tubing. These are on failed we gravel pack welled wells. We are still in the very early stages of understanding the feasibility of this and would welcome any feedback on any experience doing similar. In particular, we are worried about ECD / return rates. The wells have quite a small pore pressure frac gradient window and we will need to use a riser with over a 7” I.D. to get the Crown plugs out.
Some of the questions we have in particular are:
Do we clean up to the FPSO or the vessel? – The FPSO has the advantage of ensuring we will defiantly have the ability to stay below the frac gradient, and there is no containment issues. But has the disadvantages of potentially plugging up the tree as the well will need to be choked back, issues around control i.e. vessel in control of the tree and pumping to an FPSO that has no control of that well. Cleaning up to the vessel will come with challenges around sand disposal, as there is potential for a significant quantity. Oil disposal (in a cost effective manner, trying to avoid a full well test spread) as we are currently unable to bull head the completion volume.
Any experience on the best type of coil tools for sand clean outs – Do we jet or run a motor? If jetting is, there any risk of destabilising the formation/Gravel pack around the area of failure.
Any comments on other items would also be gratefully received.
1 Answer(s)
PLEASE LOGIN OR SIGN UP TO JOIN THE DISCUSSION
Support Spread
We need the support of our members to keep our forum online. If you find the information on spread useful please consider a donation

Posted by

Justin Hardy
Completion Engineer
Discussions: 2
Replies: 6
Related Discussions
Milling through a casing collar
With this down turn in our industry are multilaterals a useful well construction technique to reduce costs?
Expert Training Support Offer : How the Latest ERD Innovations Can Benefit Your Deviated Wells
How to remember everything you have ever learned.
Coiled tubing bridge plug milling
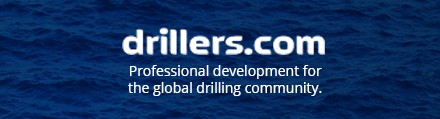
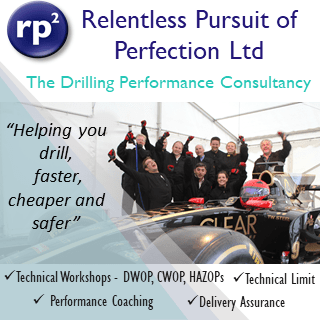