'Differential sticking' WITS case studies data for RTAS replay?
14 June 2020 Seeking any wells data available in regards to 'Differential sticking' stuck pipe events to serve to educate the next generation to take a far more proactive and prevent vs cure approach to 'manage lost time events' before they result. Where there are today excellent 'Real time drilling advisory system' that can offer the drilling safety and loss avoidance step-change warranted. Where if we can replay real well case studies and learn from these, rest assured lessons can then be incorporated into drilling programs and we educate people at the rig-site further. These events are all preventable.I'll share more recent 'differential experiences when i was last office engineering. It was not my well as I had other projects at that time.
Horizontal 8 1/2in section had been drilled in carbonates that was full of Horst and Graben (fracture) features. Where if faults/fracture interfaces are not drilled at times, by holding back on the weight and taking somewhat more time to drill these discrete formation interface (major faults fractures) changes, high-instantaneous doglegs probably result. (one of the probable causes).
There was also little evidence within in DDR's to state where these higher risked interfaces were estimated to be (e.g. as interpreted from comments within the drilling / mud logs present) Key evident indicators were therefore being missed!.
Half way through the horizontal trip out of hole a large over pull was taken, jar was fired and after a few attempts jars stopped working. As the company lead SDE at that time, my experiential advice to the projects drilling team was mechanical sticking had quickly resulted into differential sticking (as we/i had experienced this before within carbonates, on a early ERD well, circa 1990 where we had got the pipe free, twice and on other well occasions by reducing mud weight (when wellbore conditions safely permitted this). Quick response to 'do the right things' is often also paramount in such cases?
24 hrs later the team assigned was still trying to free pipe using pipe releasing agent PRA pills. Without success. A Float existed in string so a preferred U tube method could not be used. Again with further operational hrs/costs lost, advice again given was to reduce mud weight with centrifuges that were on board and every few hrs try and get the jars working. Team reluctantly agreed, several hrs later with a small mud weight achieved 0.2-0.3ppg reduction, (with balance still several hundred psi above max reservoir pressure) jar started firing and in less than 10mins string was freed.
Note: A small mud weight reduction in a high angle horizontal section can have a profound affect on reducing differential freeing forces required. i.e. often as high as 200-300K!
Later on a similar set of wells on my own project, we installed a near bit measurement tool and confirmed at such formation interfaces very high doglegs did result if drilling parameters were not controlled ( a key lesson learned). It was also clearly stated in the DDR's at what depths all interfaces were estimated to be (to be more cautious when tripping out). Where a bigger risk concern was to reduce drilling string vibration dynamic effects through drilling better wellbore cylinders so we could readily trip out on elevators (this was our primary goal) not chasing ROP. We did this on both wells in both 12 1/4" (angle building) and 8 1/2" horizontal sections. No back-reaming not once!
So if anyone is empowered to share any differential stuck pipe well case studies, with data to share?.
Please share, otherwise all stuck pipe events shall remain in the dark shadows of drilling safety, with the same lost time events probably repeated unless we as an industry can start to translate and sustain key learnings to be more proactive to prevent recurrence.
People inform us that we have the tools and the digital technologies? All we therefore need is to gather the train wreck data and replay this to learn from such events.
Can you help, what data have you to share?
Please get in touch with those in rp-squared
________________________________
Note from moderator (Dave Taylor):
- Thanks Peter for your persistent and well-intentioned attempts to tease out of our membership some of these lessons.
- This is exactly one of the reasons that I started this website in 2005.
- If members would prefer to submit their input anonymously, perhaps because their employer has something against sharing information for the benefit of the industry, then email to me (dave@rp-squared.com) and I will work with you to ensure that the data is suitably sanitised yet remains of value to our industry.
2 Answer(s)
PLEASE LOGIN OR SIGN UP TO JOIN THE DISCUSSION
Support Spread
We need the support of our members to keep our forum online. If you find the information on spread useful please consider a donation

Posted by
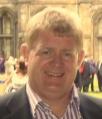
Peter Aird
Drilling Specialist/Well Engineer/Training Consultant
Discussions: 115
Replies: 449
Related Discussions
Stuck Casing on Floater
Apply torque in string when jarring down ?
Severing Drill Pipe - pipe not in tension
Stabilising formation with silicate mud
Stuck CT after screening out frac proppants in entire well
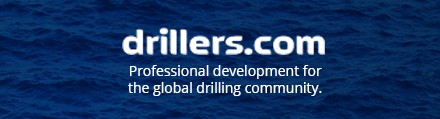
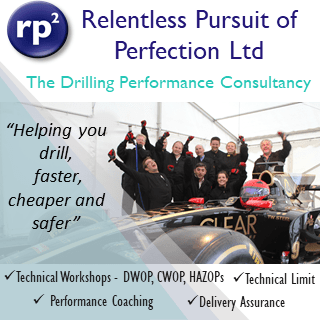