Installation of 24" conductor pipe to 30m in onshore well
16 July 2020 Dear friends in this great community,Any experience is greatly appreciated.
Our project is currently assessing various options for driving a 24" conductor pipe to 30m for a pad drilling project.
Here are a few of the key issues I would REALLY appreciate your advice on.
- We are aware that the standard length for this pie is 12m, but can 16m pipes of acceptable standard be sourced?
- Which method of connection is preferable, welding or use of couplings/ quick connection?
- For coupling, which, type of coupling is suitable?
- If coupling is used, is the significant risk of fatigue or damage due to piling and what piling parameters are preferable?
- When piling, which is the best method to minimise deviation on conductor pipe?
Lamech
5 Answer(s)
PLEASE LOGIN OR SIGN UP TO JOIN THE DISCUSSION
Support Spread
We need the support of our members to keep our forum online. If you find the information on spread useful please consider a donation

Posted by
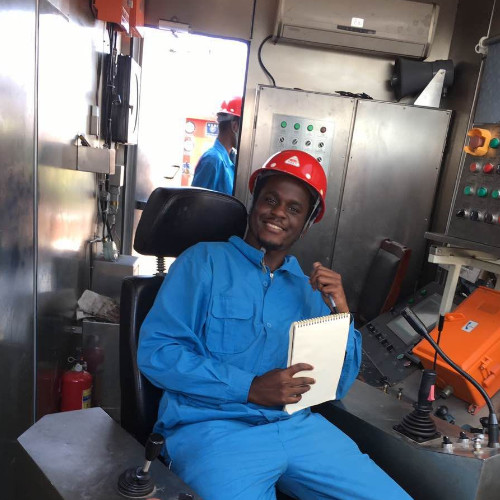
Lamech Mbangaye
Drilling Supervisor / Drilling Engineer
China National Offshore Oil Corporation
Discussions: 2
Replies: 1
Related Discussions
running conductor casing
"Green" Casing dope
Cuttings re-injection into gas lifted wells.
Inter Field Cuttings Transportation
Jack up 'Slim hole' finder well design
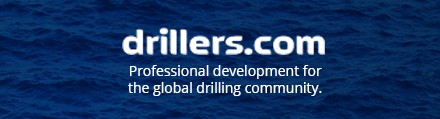
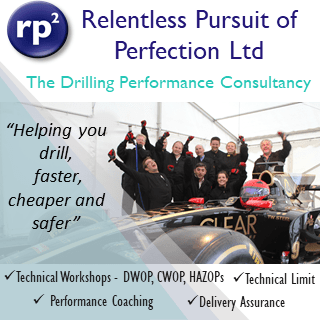