How to analyse the drillability and steerability of an extended reach well
14 August 2009 Dear Members,I need any body with experience on how to evaluate or analyse the drillability and steerability of an extended reach well, to kindly help and review, make corrections and suggestions where neccessary on my analysis of the drillability of the following extended reach well plan with a rock strength that varies from 15000psi to more than 24000psi.
Below are the analysis of the drillability and steerability of the extended reach well plan with the above range of formation strength:-
1) The first step is to determine the required hole geometry,also find out wether there are any restriction on formation stability, any interficial problems or expected torque and drag problem.
2)Determined required dog leg severity and hole quality requirements for each hole section.
3)Rotary steerable system was recommended because it gives excellent hole quality and are good up to 6degree/30meters.
4)Determined if BHA will bend around DLS without failure in rotatory mode.
5)Run Torque and Drag analysis based on the well profile and expected DLS and hole quality, to see if we can change well profile, DLS or hole quality requirements, if near limits on Torque and Drag.
6) Bit selection is based on formation to be drilled and then on the steerable system selected.
- PDC bit was preferred due to ROP, life and reliability-no bearings to fail.
-PDC with a 6inch full diameter slick gage was considered.
7)Rotory drilling mode instead of sliding drilling mode was considered because of the impossibilty of sliding drilling at extreme lateral distance.
Information involved in the extended reach well path design is as below:Torque and drag analysis allows a shallow KOP of 2100m to minimise axial stress with in the vertical depth that might cause axial vibration, my stress regime and fracture orientation allows the use of a simple build -- hold trajectory and from torque and drag analysis a sail angle of 76 degrees was calculated to minimize axial tension and friction with in the curved hole section, also my analysis called for the use of 6- 5/8in drill pipe in the upper 2755m and 5.5 in drillpipe down to the bottom hole assembly so as to minimize hydraulic friction that would limit flow rate that might lead to poor hole cleaning ,also provide the needed push to TD. Wellbore stability analysis calls for a mud weight of 1.56s.g to stabilize the trajectory, the target is located at 3033m TVD, and the horizontal departure is 2155m.
Thanks.
Divine Somiari.
0 Answer(s)
PLEASE LOGIN OR SIGN UP TO JOIN THE DISCUSSION
Support Spread
We need the support of our members to keep our forum online. If you find the information on spread useful please consider a donation

Posted by

Divine Somiari
Drilling engineer
Discussions: 3
Replies: 12
Related Discussions
Drilling 8 1/2" hole out of 20" shoe
37" HoleOpeners
Flexjoint wearbuushings
Clearing site for landrigs
Thru tubing fishing
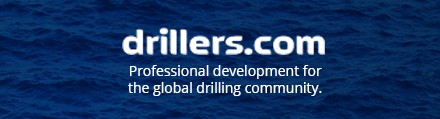
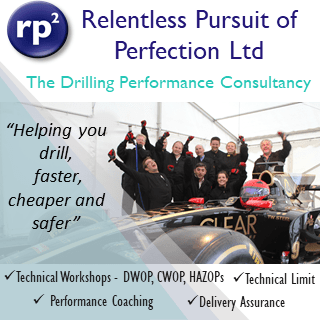