Increased Subsea BOP weights and heights to comply with API S53 BOP configuration
23 July 2020 Hi to you all,I have a couple of questions here relating to mid-water (moored) semi-subs BOPs and how the changes to reconfigure from the previous class 5 1A 4R or class 6 2A 4R to the current 1A or 2A 5R increases BOP handling height and weight.
- Do you recall what was the typical weight and height of 2A 4R subsea BOP?
- What is now a typical weight and height of a 2A 5R BOP?
- Is there any particular make/type of a 15k WP 2A 5R BOP that is the most compact and perhaps lighter in weight?
- Is there a condition that points towards deploying Subsea BOP Tethering systems. (Albeit based on the Wellhead system design or the BOP weight).
- What experience does the forum have in deploying BOP Tethering systems and what are the actual times to deploy online v offline where ever possible. (Not the marketing sale pitch times quoted by suppliers).
- Did the Tethering system dramatically reduce wellhead fatigue as originally expected or was the system not as efficient as marketed?
Ron
3 Answer(s)
PLEASE LOGIN OR SIGN UP TO JOIN THE DISCUSSION
Support Spread
We need the support of our members to keep our forum online. If you find the information on spread useful please consider a donation

Posted by

Ron Mackay
Rig Intake Advisor
Discussions: 7
Replies: 8
Related Discussions
BOP testing subsea
MS700 stuck wearbushing
Challenging subsea inspections
NOV (Shaffer) Annulars
Subsea cellar drilling to avoid icebergs.
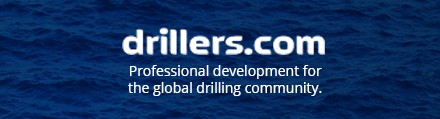
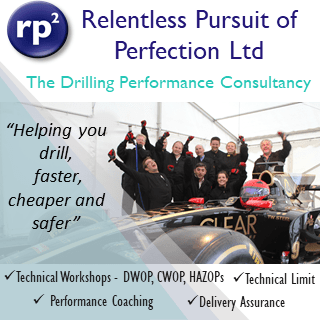