Drill Pipe backout from TD saver sub and twisted at the connection between HWDP FH and the rest of the BHA at about 5600 ft below
06 September 2019While backreaming out of hole, pumping at 1150 gpm with 120 RPM and max 30K torque, experienced total losses. Regained flow by varying rates to 200 gpm but could not backream out. String could still go down but not up. RPM was then set at 160 rpm and torque limit at 40K, string stalled and could not go up, taking a 100 k overpull. After about 5 mins, Observed string backout from saver sub and dropped into the well.
Fished the string successfully, but in two. One part was string to Jar stand crossover the other part from the HWDP to remaining of BHA. The boxend of the HWDP was seen to have some thread of the jar stand pin indicating a twist off.
What must have gone wrong?
Who has experienced this before?
17 Answer(s)
PLEASE LOGIN OR SIGN UP TO JOIN THE DISCUSSION
Support Spread
We need the support of our members to keep our forum online. If you find the information on spread useful please consider a donation

Posted by

Kingsley Okenyi
Engineer
Discussions: 1
Replies: 3
Related Discussions
Cement excess to use when Drilling-with-Casing
Performance of Volant's Casing Running Tool (CRTi)
Best parameters to drilling out cement plugs
On what parameters the suitability of UBD over MPD to drill a well can be decided.
Deepwater Drilling Joint Industry Project Event
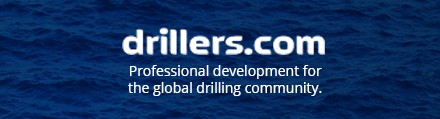
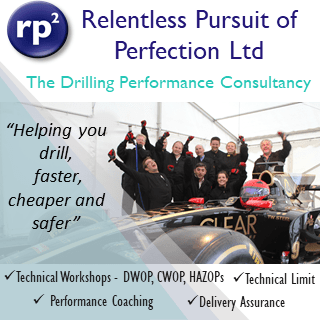