Cement excess to use when Drilling-with-Casing
22 March 2019 Dear allAs a further derivation of a previous thread (https://my-spread.com/discussions/6392),
here's one to get your teeth into.
At a recent DWOP that we facilitated (our 438th Workshop!!), one of the groups was challenged to decide what cement excess to use for a 13⅜" casing (drilled with 17" OD drill-shoe). It is required to get cement to seabed, because the HP wellhead housing will be installed on the top off this casing (swedged over).
The thread that I referred to above (6392) asks several questions, including how to determine excess to use when there is no caliper information available.
We do plan to pump a fluid caliper, but I'm left wondering what technology is out there and/or what empirical data you might have based on actual cement jobs conducted.
Many thanks
Dave
4 Answer(s)
PLEASE LOGIN OR SIGN UP TO JOIN THE DISCUSSION
Support Spread
We need the support of our members to keep our forum online. If you find the information on spread useful please consider a donation

Posted by
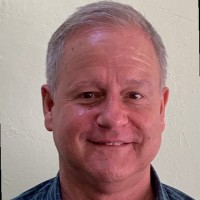
Dave Taylor - SPREAD Moderator
Managing Director (rp-squared.com)
Relentless Pursuit Of Perfection Ltd.
Discussions: 232
Replies: 347
Related Discussions
Performance of Volant's Casing Running Tool (CRTi)
Drill Pipe backout from TD saver sub and twisted at the connection between HWDP FH and the rest of the BHA at about 5600 ft below
Best parameters to drilling out cement plugs
On what parameters the suitability of UBD over MPD to drill a well can be decided.
Deepwater Drilling Joint Industry Project Event
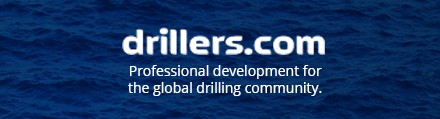
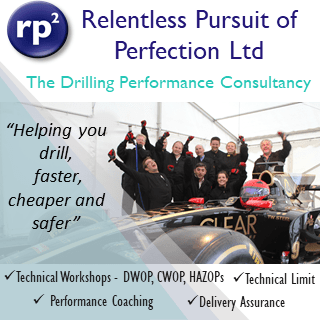