Spudding offshore riserless with a mud motor ?
17 August 2020 Another bone of contention that I would be interested to gather others ‘Evidence based points of view‘.Would be.
Sharing EVIDENT pros and cons to spudding, ie drilling and cement an offshore well’s conductor and surface string where subsurface conditions cannot afford jetting a conductor.
Northern Southern Hemisphere areas, other regions where non-jettable ) hard ground, sand carbonate dominant etc) subsurface conditions may exist.
What is optimal ?
MOTOR vs Rotary assembly.?
What is optimal ?
MOTOR vs Rotary assembly.?
Why is this evidently so?
What does your wells data show/state experience prove ?
Evident Case study wells examples to share?
What set up, has repeatedly and more consistently delivered best process safety, optimal, higher quality, less problematical drilling solutions.
Why was this evidently so?
Looking forward to members sharing evident views on this highly debatable subject,
Note: Ask the big three service companies? they will always try and sell and tell that a motor solution is best? .
Despite the Substance and evidence warranted? to be checked and assessed to back this up.
8 Answer(s)
PLEASE LOGIN OR SIGN UP TO JOIN THE DISCUSSION
Support Spread
We need the support of our members to keep our forum online. If you find the information on spread useful please consider a donation

Posted by
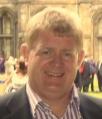
Peter Aird
Drilling Specialist/Well Engineer/Training Consultant
Discussions: 115
Replies: 449
Related Discussions
Multiple drilling then casing/cementing?
17 1/2" riserless drilling
Automated rigs - pros and cons
Semi-Sub Operational Effectiveness
How this site is paid for : excellent performance support from rp-squared
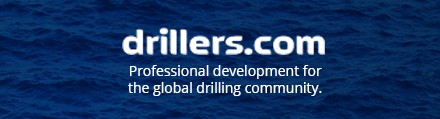
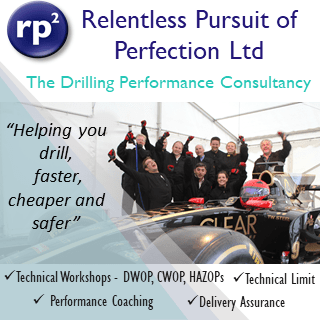